Scenario Acme engineering is a general light engineering company that specializes in metallic fixtures and fittings. It manufactures various products to customer order, and also has long term contracts to supply manufactured products to other companies. Acme is a “jobbing shop” involving craftspeople making specialized complete products – it is not a production line operation. The craftspeople work on early (6am – 2pm) and late (2pm – 10pm) shifts 5 days a week, and sometimes do overtime on Saturdays. The factory is always closed on Sundays. Each shift has a supervisor. The management team consists of the Managing Director (MD), Accountant and Sales Manager. They are assisted by two Administrative Assistants who work Monday to Friday, 8.30am to 5.30pm. The management team has decided that, in order to become more competitive, it needs more and better information on the costs involved in manufacturing. It wants to build up a database of time and cost information per manufacturing job, so that future work can be priced more accurately. This will involve recording the time spent on each manufacturing job, the costs of materials used, and the overhead costs. One problem is that Acme’s craftspeople have always had a free hand to carry out their work however they like, as long as the finished fixtures and fittings conform to specification and meet deadlines. The MD has engaged an IT consultancy company to analyze the requirements and design a system to meet them. The team will include a consultant with extensive experience of implementing manufacturing control systems. Acme has provided the following list of requirements to the consultancy company: 1. The system is to log the craftsperson, start and finish time and materials used for each manufacturing job. This must be possible on all shifts, including overtime. 2. The data for time and materials used is to be captured on touch screens next to the machines on the factory floor so that the craftsperson’s work is not disrupted. This facility is to be usable in a noisy and dirty workshop environment. 3. The system is to calculate material costs and overhead costs incurred for each manufacturing job. 4. The system is to provide a “time spent” analysis (time to set up, time per step, rework time) report of the work done by each craftsperson. 5. The managing director would like a data mining type function to drill down on historic data and look at costs in total, or per product range, or per product type, or per craftsperson, over a flexible period of time, or for an individual piece of work. 6. The sales manager has asked for secure remote access via VPN using a laptop to the historic data on the system when working away from the office. Question 1: From requirements 1 to 6 (or parts thereof) on the previous page, give one example of each of the following, justifying your selection in each case: Two functional requirements Two non-functional requirements Two ambiguous requirements Two requirements in conflict with each other (i.e., one conflict across 2 requirements)
Scenario Acme engineering is a general light engineering company that specializes in metallic fixtures and fittings. It manufactures various products to customer order, and also has long term contracts to supply manufactured products to other companies. Acme is a “jobbing shop” involving craftspeople making specialized complete products – it is not a production line operation. The craftspeople work on early (6am – 2pm) and late (2pm – 10pm) shifts 5 days a week, and sometimes do overtime on Saturdays. The factory is always closed on Sundays. Each shift has a supervisor. The management team consists of the Managing Director (MD), Accountant and Sales Manager. They are assisted by two Administrative Assistants who work Monday to Friday, 8.30am to 5.30pm. The management team has decided that, in order to become more competitive, it needs more and better information on the costs involved in manufacturing. It wants to build up a
1. The system is to log the craftsperson, start and finish time and materials used for each manufacturing job. This must be possible on all shifts, including overtime.
2. The data for time and materials used is to be captured on touch screens next to the machines on the factory floor so that the craftsperson’s work is not disrupted. This facility is to be usable in a noisy and dirty workshop environment.
3. The system is to calculate material costs and overhead costs incurred for each manufacturing job.
4. The system is to provide a “time spent” analysis (time to set up, time per step, rework time) report of the work done by each craftsperson.
5. The managing director would like a data mining type function to drill down on historic data and look at costs in total, or per product range, or per product type, or per craftsperson, over a flexible period of time, or for an individual piece of work.
6. The sales manager has asked for secure remote access via VPN using a laptop to the historic data on the system when working away from the office.
Question 1:
From requirements 1 to 6 (or parts thereof) on the previous page, give one example of each of the following, justifying your selection in each case:
Two functional requirements
Two non-functional requirements
Two ambiguous requirements
Two requirements in conflict with each other (i.e., one conflict across 2 requirements)
Question 2:
Identify three (3) different stakeholders or stakeholder groups whose requirements must be explored. In each case, identify which elicitation technique would be appropriate and provide a justification to support your selection.

Trending now
This is a popular solution!
Step by step
Solved in 4 steps

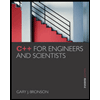
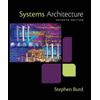

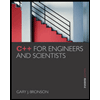
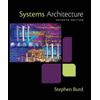
