In this assignment, a back pressure cogeneration plant process (see Figure 1) producing district heat (DH) and electricity will be designed based on given supply and return water temperatures and DH production. Personal initial values are listed in Appendix 1, plant and component efficiency assumptions and pressure drops are listed in Table 1. Using the given and chosen values, • determine pressure, temperature, specific enthalpy, and mass flow rate at each state point • calculate net electric power, fuel consumption, and efficiencies for electricity and CHP production • draw the process in a T,s-diagram (boiler pressure drop is assumed to occur entirely in superheaters) fuel air HPPH Boll 7 Efficiencies 6 E1 E12 Pressure drops FWP Table 1. Efficiencies and pressure losses E1 DA 5 Turbine E2 2 DHC 3 € supply return CP Figure 1. A process diagram for a back pressure CHP plant; G = generator, B = boiler, DA = deaerator (open feed heater), DHC = district heating condenser, HPPH = high pressure pre-heater (closed feed heater), CP = condensate pump, FWP = feed water pump, deaerator (open heater), Is = live steam, E = extraction. superheated steam wet steam saturated liquid subcooled liquid DH water air fuel flue gas Boiler efficiency = 0.90 Turbogenerator electromechanical efficiency 77mg = 0.98 Transformer efficiency nu = 0.99 Auxiliary power efficiency = 0.93 Turbine overall isentropic expansion efficiency n = 0.85 Feedwater pump compression efficiency FWP = 0.80 Condensate pump: enthalpy increase assumed Ahcp≈ 1 kJ/kg HP feed heater, steam side: 5 % HP feed heater, water side: 0.4 bar Boiler: 15% of live steam (state point Is) pressure Main condensate, feed water and extraction steam pipes: Ap≈ 0 Some of the initial values are given. The rest must be chosen based on lectures, material provided in Moodle, and other resources. The specific enthalpy increase Ah in preheaters must be chosen optimally for maximum process efficiency (see Lecture 2 slides and L2 example 2).
In this assignment, a back pressure cogeneration plant process (see Figure 1) producing district heat (DH) and electricity will be designed based on given supply and return water temperatures and DH production. Personal initial values are listed in Appendix 1, plant and component efficiency assumptions and pressure drops are listed in Table 1. Using the given and chosen values, • determine pressure, temperature, specific enthalpy, and mass flow rate at each state point • calculate net electric power, fuel consumption, and efficiencies for electricity and CHP production • draw the process in a T,s-diagram (boiler pressure drop is assumed to occur entirely in superheaters) fuel air HPPH Boll 7 Efficiencies 6 E1 E12 Pressure drops FWP Table 1. Efficiencies and pressure losses E1 DA 5 Turbine E2 2 DHC 3 € supply return CP Figure 1. A process diagram for a back pressure CHP plant; G = generator, B = boiler, DA = deaerator (open feed heater), DHC = district heating condenser, HPPH = high pressure pre-heater (closed feed heater), CP = condensate pump, FWP = feed water pump, deaerator (open heater), Is = live steam, E = extraction. superheated steam wet steam saturated liquid subcooled liquid DH water air fuel flue gas Boiler efficiency = 0.90 Turbogenerator electromechanical efficiency 77mg = 0.98 Transformer efficiency nu = 0.99 Auxiliary power efficiency = 0.93 Turbine overall isentropic expansion efficiency n = 0.85 Feedwater pump compression efficiency FWP = 0.80 Condensate pump: enthalpy increase assumed Ahcp≈ 1 kJ/kg HP feed heater, steam side: 5 % HP feed heater, water side: 0.4 bar Boiler: 15% of live steam (state point Is) pressure Main condensate, feed water and extraction steam pipes: Ap≈ 0 Some of the initial values are given. The rest must be chosen based on lectures, material provided in Moodle, and other resources. The specific enthalpy increase Ah in preheaters must be chosen optimally for maximum process efficiency (see Lecture 2 slides and L2 example 2).
Power System Analysis and Design (MindTap Course List)
6th Edition
ISBN:9781305632134
Author:J. Duncan Glover, Thomas Overbye, Mulukutla S. Sarma
Publisher:J. Duncan Glover, Thomas Overbye, Mulukutla S. Sarma
Chapter2: Fundamentals
Section: Chapter Questions
Problem 2.31P: Consider two interconnected voltage sources connected by a line of impedance Z=jX, as shown in...
Related questions
Question

Transcribed Image Text:In this assignment, a back pressure cogeneration plant process (see Figure 1) producing district
heat (DH) and electricity will be designed based on given supply and return water
temperatures and DH production. Personal initial values are listed in Appendix 1, plant and
component efficiency assumptions and pressure drops are listed in Table 1. Using the given
and chosen values,
• determine pressure, temperature, specific enthalpy, and mass flow rate at each state point
• calculate net electric power, fuel consumption, and efficiencies for electricity and CHP
production
• draw the process in a T,s-diagram (boiler pressure drop is assumed to occur entirely in
superheaters)
fuel
air
HPPH
Boll
7
Efficiencies
6
E1
E12
Pressure drops
FWP
Table 1. Efficiencies and pressure losses
E1
DA
5
Turbine
E2
2
DHC
3
€
supply
return
CP
Figure 1. A process diagram for a back pressure CHP plant; G = generator, B = boiler, DA = deaerator
(open feed heater), DHC = district heating condenser, HPPH = high pressure pre-heater (closed feed heater),
CP = condensate pump, FWP = feed water pump, deaerator (open heater), Is = live steam, E = extraction.
superheated steam
wet steam
saturated liquid
subcooled liquid
DH water
air
fuel
flue gas
Boiler efficiency = 0.90
Turbogenerator electromechanical efficiency 77mg = 0.98
Transformer efficiency nu = 0.99
Auxiliary power efficiency = 0.93
Turbine overall isentropic expansion efficiency n = 0.85
Feedwater pump compression efficiency FWP = 0.80
Condensate pump: enthalpy increase assumed Ahcp≈ 1 kJ/kg
HP feed heater, steam side: 5 %
HP feed heater, water side: 0.4 bar
Boiler: 15% of live steam (state point Is) pressure
Main condensate, feed water and extraction steam pipes: Ap≈ 0
Some of the initial values are given. The rest must be chosen based on lectures, material
provided in Moodle, and other resources. The specific enthalpy increase Ah in preheaters must
be chosen optimally for maximum process efficiency (see Lecture 2 slides and L2 example 2).
AI-Generated Solution
Unlock instant AI solutions
Tap the button
to generate a solution
Recommended textbooks for you
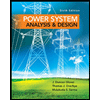
Power System Analysis and Design (MindTap Course …
Electrical Engineering
ISBN:
9781305632134
Author:
J. Duncan Glover, Thomas Overbye, Mulukutla S. Sarma
Publisher:
Cengage Learning
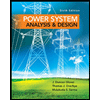
Power System Analysis and Design (MindTap Course …
Electrical Engineering
ISBN:
9781305632134
Author:
J. Duncan Glover, Thomas Overbye, Mulukutla S. Sarma
Publisher:
Cengage Learning