Grainger: Reengineering the China/ W. W. Grainger, Inc., is a leading supplier of maintenance, repair, and operating (MRO) products to businesses and institutions United States, Canada, and Mexico, with an expanding presence in Japan, India, China, and Panama. The company works with m than 5,000 suppliers and runs an extensive website (www.grainger.com) where Grainger offers nearly 1.5 million products. The products range from industrial adhesives used in manufacturing, to hand tools, janitorial supplies, lighting equipment, and power When something is needed by one of its customers, it is often needed quickly, so quick service and product availability are key d to Grainger's success.
Grainger: Reengineering the China/ W. W. Grainger, Inc., is a leading supplier of maintenance, repair, and operating (MRO) products to businesses and institutions United States, Canada, and Mexico, with an expanding presence in Japan, India, China, and Panama. The company works with m than 5,000 suppliers and runs an extensive website (www.grainger.com) where Grainger offers nearly 1.5 million products. The products range from industrial adhesives used in manufacturing, to hand tools, janitorial supplies, lighting equipment, and power When something is needed by one of its customers, it is often needed quickly, so quick service and product availability are key d to Grainger's success.
Purchasing and Supply Chain Management
6th Edition
ISBN:9781285869681
Author:Robert M. Monczka, Robert B. Handfield, Larry C. Giunipero, James L. Patterson
Publisher:Robert M. Monczka, Robert B. Handfield, Larry C. Giunipero, James L. Patterson
ChapterC: Cases
Section: Chapter Questions
Problem 1.1A: Avion, Inc. Susan Dey and Bill Mifflin, procurement managers at Avion, Inc., sat across from each...
Related questions
Question

Transcribed Image Text:Grainger: Reengineering the China/U.S. Supply Chain
W. W. Grainger, Inc., is a leading supplier of maintenance, repair, and operating (MRO) products to businesses and institutions in the
United States, Canada, and Mexico, with an expanding presence in Japan, India, China, and Panama. The company works with more
than 5,000 suppliers and runs an extensive website (www.grainger.com) where Grainger offers nearly 1.5 million products. The
products range from industrial adhesives used in manufacturing, to hand tools, janitorial supplies, lighting equipment, and power tools.
When something is needed by one of its customers, it is often needed quickly, so quick service and product availability are key drivers
to Grainger's success.
Your assignment involves studying U.S. distribution in Grainger's supply chain. Grainger works with over 250 suppliers in the China
and Taiwan region. These suppliers produce products to Grainger's specifi cations and ship to the United States using ocean freight
carriers from four major ports in China and Taiwan. From these ports, product is shipped to U.S. entry ports in either Seattle,
Washington, or Los Angeles, California. After passing through customs, the 20- and 40-foot containers are shipped by rail to Grainger's
central distribution center in Kansas City, Kansas. The containers are unloaded and quality is checked in Kansas City. From there,
individual items are sent to regional warehouses in nine U.S. locations, a Canada site, and Mexico.
Grainger: U.S. Distribution
In the United States approximately 40 percent of the containers enter in Seattle, Washington, and 60 percent at the Los Angeles,
California, port. Containers on arrival at the port cities are inspected by federal agents and then loaded onto rail cars for movement to
the Kansas City distribution center. Variable costs for processing at the port are $7.00 per cubic meter (CBM) in both Los Angeles and
Seattle. The rate for shipping the containers to Kansas City is $0.0018 per CBM per mile.
In Kansas City the containers are unloaded and processed through a quality assurance check. This costs $6.00 per CBM processed. A
very small percentage of the material is actually sent back to the supplier, but errors in quantity and package size are often found that
require accounting adjustments.
Items are stored in the Kansas City distribution center, which serves nine warehouses in the United States. Items are also sent to
warehouses in Canada and Mexico, but for the purposes of this study we focus on the United States. The nine warehouses each place
orders at the distribution center that contains all the items to be replenished. Kansas City picks each item on the order, consolidates
the items onto pallets, and ships the items on 53-foot trucks destined to each warehouse. Truck freight costs $0.0218 per CBM per
mile. The demand forecasts for the items purchased from China/Taiwan for next year in cubic meters and shipping distances are given
in the following table.
DEMAND (CBM)
WAREHOUSE
Kansas City
Cleveland
Newark
Jacksonville
AVERAGE
DISTANCES
MILES FROM KANSAS CITY MILES FROM LOS ANGELES MILES FROM SEATTLE
20,890
0
1,650
1,800
17,100
830
2,380
2,310
24,730
1,230
2,730
2,750
15,120
1,170
2,480
2,950
Chicago
22,870
470
1,980
1,990
Greenville
15,120
970
2,370
2,950
Memphis
17,150
460
1,780
2,370
Dallas
22,870
450
1,420
2,160
Los Angeles
34,100
1,650
e
1,140
Total
189,950

Transcribed Image Text:Although a high percentage of demand was from warehouses either south or east of Kansas City, the question has surfaced
concerning the 34,100 CBM (approximately 18 percent of the total volume) that will be shipped to Kansas City and then shipped back
to the Los Angeles warehouse. This double-transportation could potentially be eliminated if a new distribution center were built in Los
Angeles. The idea might be to ship material arriving at the Seattle port by rail to a new Los Angeles distribution center, which would be
located at the current location of the Los Angeles warehouse.
It is estimated that the Los Angeles facility could be upgraded at a one-time cost of $1,500,000 and then operated for $350,000 per
year. In the new Los Angeles distribution center, containers would be unloaded and processed through a quality assurance check, just
as is now done in Kansas City. The variable cost for doing this would be $7.00 per CBM processed, which includes the cost to move
the containers from the Los Angeles port to the distribution center.
After the material is processed in Los Angeles, the amount needed to replenish the Los Angeles warehouse (34,100 CBM per year on
average) would be kept and the rest sent by rail to Kansas City. It would then be directly stocked in the Kansas City distribution center
and used to replenish the warehouses. They expect that very little would need to be shipped back to the Los Angeles warehouse after
the new system was operating for about six months.
Grainger management feels that it may be possible to make this change, but they are not sure if it would actually save any money and
whether it would be a good strategic change.
*The data in this case have been developed for teaching purposes and do not represent the actual situation at Grainger. The data,
though, are representative of an actual problem that Grainger and similar companies must address to efficiently run the supply chain.
Relative to the U.S. distribution network, calculate the cost associated with running the existing system. Assume that 40 percent of the
volume arrives in Seattle and 60 percent in Los Angeles and the port processing fee for federal processing at both locations is $7.00
per CBM. Assume that everything is transferred to the Kansas City distribution center by rail, where it is unloaded and quality checked.
Assume that all volume is then transferred by truck to the nine existing warehouses in the United States. (Do not round intermediate
calculations and round your answers to the nearest whole number.)
Expert Solution

This question has been solved!
Explore an expertly crafted, step-by-step solution for a thorough understanding of key concepts.
This is a popular solution!
Trending now
This is a popular solution!
Step by step
Solved in 4 steps with 8 images

Recommended textbooks for you
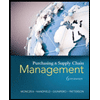
Purchasing and Supply Chain Management
Operations Management
ISBN:
9781285869681
Author:
Robert M. Monczka, Robert B. Handfield, Larry C. Giunipero, James L. Patterson
Publisher:
Cengage Learning
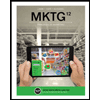
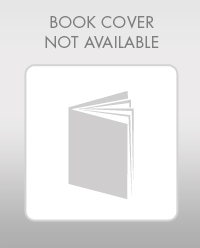
Contemporary Marketing
Marketing
ISBN:
9780357033777
Author:
Louis E. Boone, David L. Kurtz
Publisher:
Cengage Learning
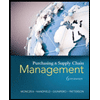
Purchasing and Supply Chain Management
Operations Management
ISBN:
9781285869681
Author:
Robert M. Monczka, Robert B. Handfield, Larry C. Giunipero, James L. Patterson
Publisher:
Cengage Learning
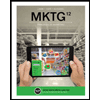
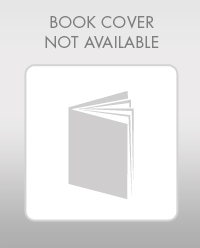
Contemporary Marketing
Marketing
ISBN:
9780357033777
Author:
Louis E. Boone, David L. Kurtz
Publisher:
Cengage Learning